Inert Gas Systems
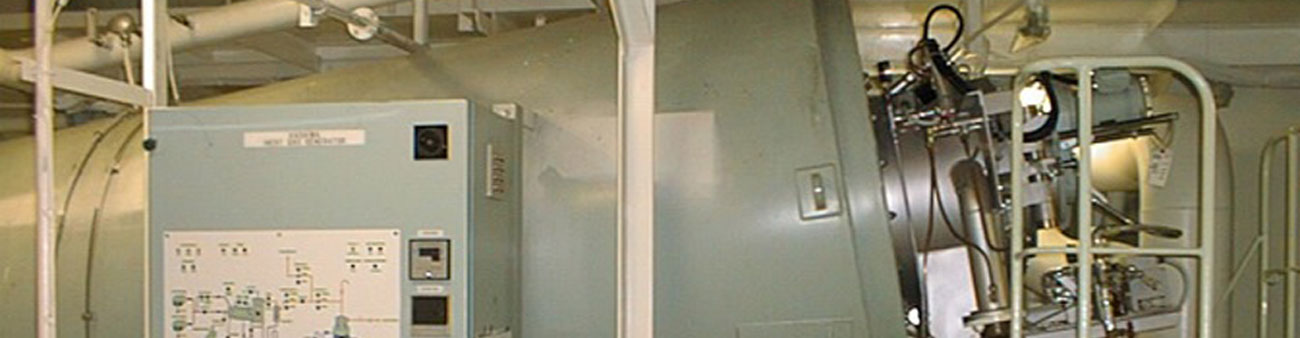
Inert Gas Systems Required for Tankers for Explosion Protection
SOLAS convention (International Convention for the Safety of Life at Sea) adopted in 1970 by IMO (International Maritime Organization) requires filling inert gas into the free space of cargo tanks of tankers carrying flammable substances such as crude oil to prevent accidental ignition and explosion. Ahead of the times, Kashiwa started offering the inert gas systems since 1970 and has so far delivered them to nearly 1900 ships.
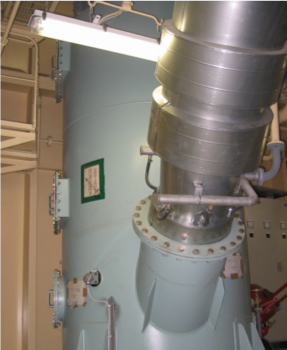
Principles of Explosion Protection
In general, three conditions need to be met at the same time for explosion to occur; presence of ignition source, flammables and oxygen. Explosion of cargos is likely expected when an ignition source (e.g. spark) is present in cargo tanks where flammable gasses and oxygen are mixed in high concentration. In other words, explosion can be controlled or prevented as far as oxygen concentration is kept low enough even if a spark is stricken. The inert gas systems thereby fill the free space in cargo tanks with the inert gas and lower the oxygen concentration in the tanks to prevent fires and explosion, ensuring safety of the crew and the ship.
Types of Inert Gas Systems
Comparison of Inert Gas Systems | ||||
---|---|---|---|---|
Adaptability | IGS | IGG | Membrane N2 | PSA N2 |
Crude oil tankers | ◯ | △ | ▲ | ▲ |
Utilizes the exhaust gas from boilers. The most economical. | Burns fuels to generate cleaner inert gas, but less economical than IGS. | Generates much cleaner inert gas than IGS/IGG, which does not necessary for crude oil tankers. Less cost effective. | ||
Product tankers | △ | ◯ | ◯ | ◯ |
Produces impurities entrained in the inert gas generated by combustion process. Care should be taken not to contaminate the cargos. | Generates cleaner inert gas than IGS by combustion process which inevitably produces small amount of impurities. | Generates much cleaner inert gas which gives less impact on the cargos, but is more costly than IGS/IGG. | ||
Chemical tankers | ▲ | △ | ◯ | ◯ |
Not recommended since contamination of the cargos with the impurities in the inert gas is highly expected. | Recommended since much cleaner inert gas with very low oxygen content can be generated. |
We have four types of the system available: Inert Gas System utilizing the exhaust gas from boilers, Inert Gas Generator System burning fuel oil separately to generate combustion gas with low oxygen content, and two different N2 Generator Systems which separate N2 from air.
The latter can generate cleaner inert gas than the former one. Various systems are available for your ships depending on the flammable substances to carry, such as crude oil or high-purity chemical products.
N2 Generator Systems – Membrane and PSA
Membrane N2 Generator System | PSA N2 Generator System | |
---|---|---|
Equipment overview | ![]() | ![]() |
Configuration | Compressor Air treatment system (filters) Purging (unnecessary gasses) Membrane N2 gas (95~99.9% purity) | Compressor Air treatment system (filters) Purging (unnecessary gasses) Adsorption columns N2 gas (95~99.99% purity) |
N2 generation | Employs the difference of the permeability through the membrane to separate N2 from other gasses in the air. | Employs the difference of the adsorption characteristic to the porous adsorbing materials to separate N2 from other gasses in the air. |
Control | Pressurized air is filtered to remove dusts and continuously fed to the membrane to extract high-concentration N2 gas that does not permeate the membrane. | Pressurized air is filtered to remove dusts and fed to the adsorption columns to extract high-concentration N2 gas that is not adsorbed. Pressurization/adsorption and depressurization/desorption process are alternately repeated in the two columns to reactivate the adsorption materials. |
Purity | High (~99.9%) | Ultra-high (~99.99%) |
Capacity | 95% purity: 70~4,500Nm3/h (discharge pressure: approx.1.1MPa) 99.9% purity: max. 540Nm3/h (discharge pressure: approx.1.1MPa) | 95% purity: 10~4,500Nm3/h (discharge pressure: approx.0.7MPa) 99.9% purity: max. 1,500Nm3/h (discharge pressure: approx.0.7MPa) |
Power consumption | High; air needs to get pressurized to 10~15bar | Low; air needs to get pressurized to 7~10bar |
Installation | The system consists of separated several modules, enabling flexible installation even in small spaces. | The system is heavier and requires much space. |
Maintenance | Its simple control and configuration require less maintenance. | It has a lot of automatic control valves which require more complicated maintenance than the membrane system. |
Running cost | Almost the same as PSA at 95% purity, but goes up as the purity is elevated. | Lower at higher purity |